Vitrintec’s green side
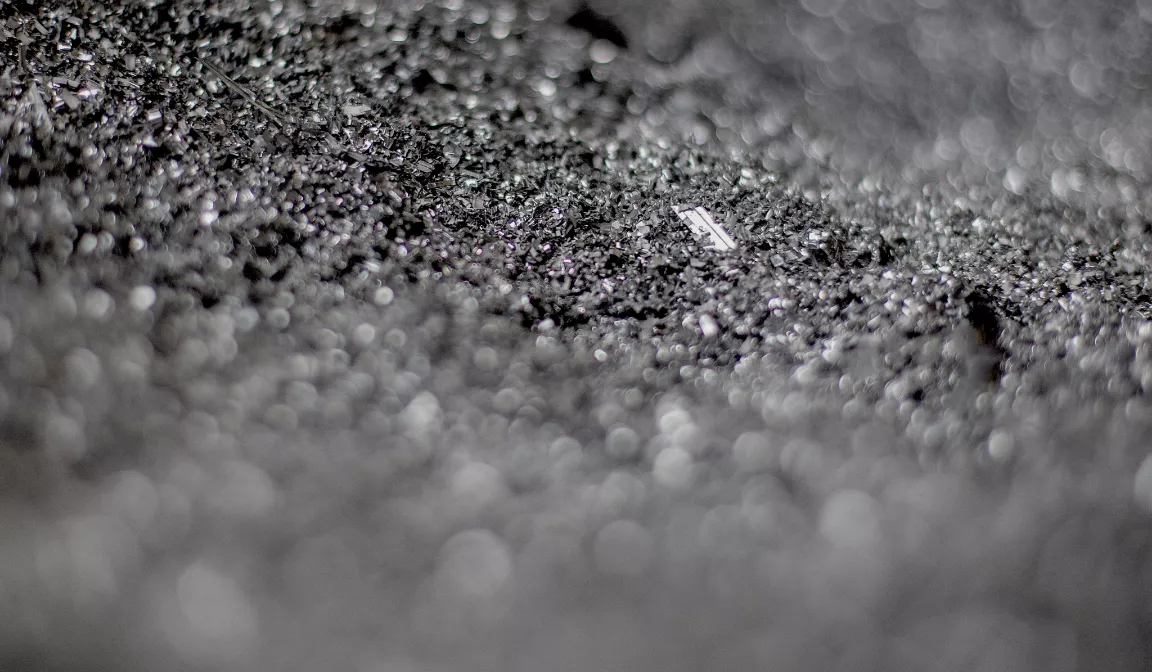
Recycling is simply a method of environmental protection. It involves recovering raw materials from waste products and using them to produce new, sought-after goods. Along with glass and steel, aluminium is one of the most easily recyclable materials on the planet. Almost 75 per cent of all aluminium ever produced is still in use today; most of the cans you buy in the shop have already been recycled many times.
Aluminium is the backbone of Vitrintec’s business and allows us to expand our nature-focused activities. However, the practical and environmentally friendly aspect of aluminium does not mean it is easy to manufacture. Its manufacture requires significant amounts of energy. Extracting and refining aluminium from mined bauxite ore and producing pure aluminium is, according to Pieterjan Van Uytvanck and Uday Patel of Forbes, a “complicated, costly and energy-intensive” process. Van Uytvanck and Patel calculated that it takes an average of 14,000 kWh of electricity to produce just one tonne of this metal. At Vitrintec, we have also dealt with the need to consume the large amount of energy required for production. Environmental concern dictates our every action, so we use green energy from photovoltaic cells to power our production halls. At the same time, we only use energy-efficient tools. While the environmental impact of aluminium production can be significant, the benefits of recycling aluminium are clear. The reason three-quarters of all aluminium ever produced is still in use is simple; its recycling represents the closed-loop economy at its best.
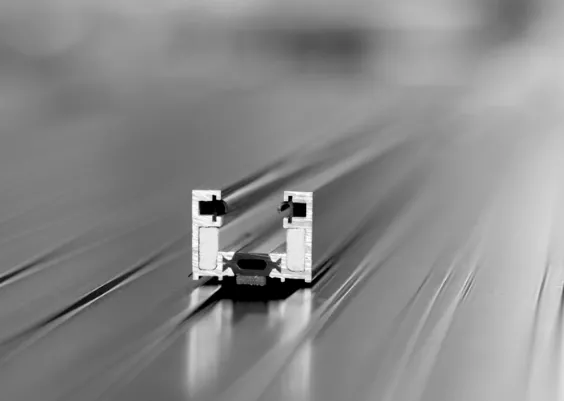
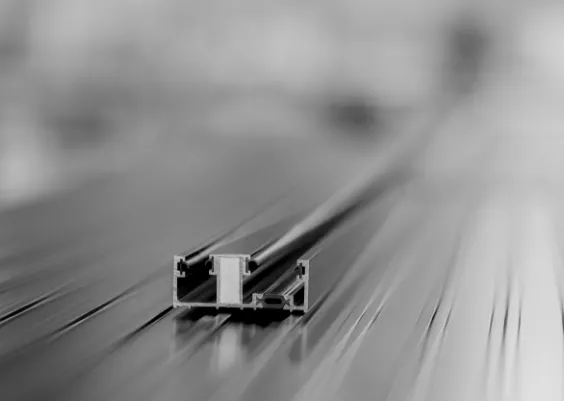
Aluminium is one of the most recycled materials in the world and one of the easiest to recycle. So what is the aluminium recycling process, and how is the metal recovered in the first place?
Aluminium is recycled by shredding into chips and passing through an infrared sorter to remove any plastic, glass or other contaminants, followed by a magnet that picks up any steel scraps. The aluminium chips are then melted at about 660.3 °C to a liquid state and poured into large moulds to produce ingots. During the remelting process, the paint and varnish on the aluminium profiles evaporate, and when the chips melt and react with the air, an aluminium oxide called dross is formed. To remove the dross, the kiln operator uses a large, machine-driven paddle to collect this dross from the top. This dross is collected and then goes through its own aluminium recycling process to remove residual aluminium oxide.
Why is 75 per cent of all aluminium ever produced still in use?
There is a simple and economic reason for this. Although the extraction and refining of virgin aluminium from mined bauxite ore are costly and energy-intensive, recycling scrap metal requires only five per cent of the energy needed to produce it, resulting in a 95 per cent energy saving when using recycled aluminium instead of virgin material: a rarity in “this world”. Before widespread commercial recycling, aluminium was one of the planet’s most expensive metals, more so than gold. For the most part, aluminium recycling rates worldwide have steadily improved. The Aluminium Association’s report of September 2019 found that the industry’s recycling rate is 63.6%.
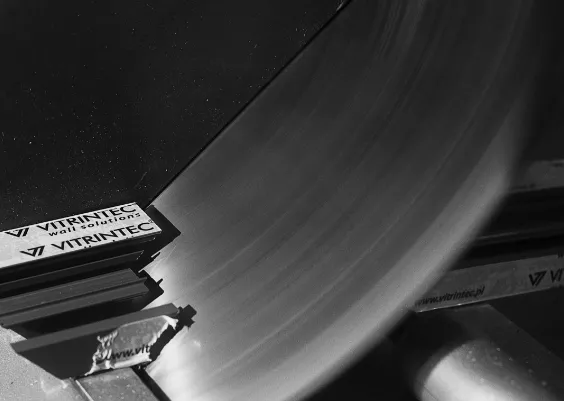
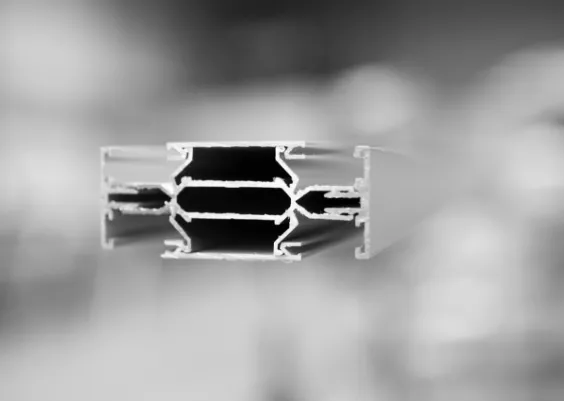
The future of aluminium recycling
While aluminium prices have fluctuated in recent years due to geopolitical issues affecting supply, the future of recycling remains bright. Aluminium, one of the more stable commodities in the recycling stream, has led many big names in the construction or food sector to choose it. All processes carried out at Vitrintec are developed with energy and material efficiency in mind. The profiles we produce are the lowest available on the market, so aluminium consumption is reduced to a minimum. This is one of many concessions to nature. Since the beginning, our company has operated in line with the principles of sustainable production. In addition, we work using energy-efficient tools. As a modern and environmentally conscious company, we fulfil our sustainable building goals by fully recycling all waste. We are constantly developing and educating ourselves in the area of climate policy measures.